There are cheaper, less time consuming alternatives to CFD surrogate models, writes HydroComp’s Don MacPherson.
This article has been reprinted with permission from the October 2020 issue of The Naval Architect.
One tool in an operator’s hunt for fuel reduction is trim optimization. Simply put, this is the setting of a ship on a waterline – different from its design waterline – that will offer a reduction in power demand and fuel consumption. It is an interesting proposition, but one that must be undertaken by both operators and designers with an appreciation for the constraints of a trimmed operation, as well as the uncertainties in the prediction of power under trimmed conditions.
The first question that I would ask is “what compromises are being made if I run trimmed?” Ship operation is more than just the economics of fuel consumption. Other considerations that may prohibit trimmed operation include:
- Reduction in visibility
- Emergence of the propeller
- Seakeeping, motions, or shipped water on deck
- Underkeel clearance
- Hull loading and strength
Once it has been satisfied that these restrictions can be met, only then will it make sense to look into benefits of trimmed operation and find an “optimum trim”. Let me first propose that there is no such thing as “optimum” in naval architecture. Everything is a compromise, but we definitely can find what is “better”.
In most cases, trim optimization studies focus on the reduction in ship resistance, which makes sense given that this is the principal demand on the system. Power and fuel are the response to that demand. However, there can be variations in propulsor efficiency with trimmed operation (particularly with bow down operation) that should be investigated as part of the study using a system tool such as NavCad® for full Vessel-Propulsor-Drive prediction of fuel.
Many trim optimization studies are based on CFD “surrogate models” whereby a matrix of loadings and trims are calculated to provide a way to interpolate a prediction. As you might expect, this can be a costly and time-consuming set of calculations, as many combinations of draft, trim, and speed are needed to create the matrix of results. That said, it is a strategic calculation that should need to be conducted just once. Let me also note that confidence in complex analytical computations can be masked by a lack of benchmarking or validation, and CFD calculations are no exception. For example, let me quote opposing conclusions from two published CFD studies of trim optimization for the well-known KRISO Container Ship (KCS).
- “The effect on resistance is varying during stern trim and optimum trim point is 0.02m trim by stern.” (This TNA Oct 2020 Trim Optimisation using NavCad for prediction confidenceis about 0.15 degrees for about a 2.2% drag reduction.)
- “The free model can accurately predict the 1% reduction in total resistance when the ship is trimmed 0.25 degree by bow.”
Not a great confidence builder… so let’s then consider the benefit of reduced-order calculations that have some semi-empirical basis, again such as those available in NavCad. Often called 1D and 2D methods, parametric methods (1D) and NavCad’s Analytical Distributed Volume Method (ADVM, a 2D method) provide efficient alternatives or companions to CFD (3D). Can these methods provide a sufficiently accurate option for prediction of trimmed operation? Well, yes and no.
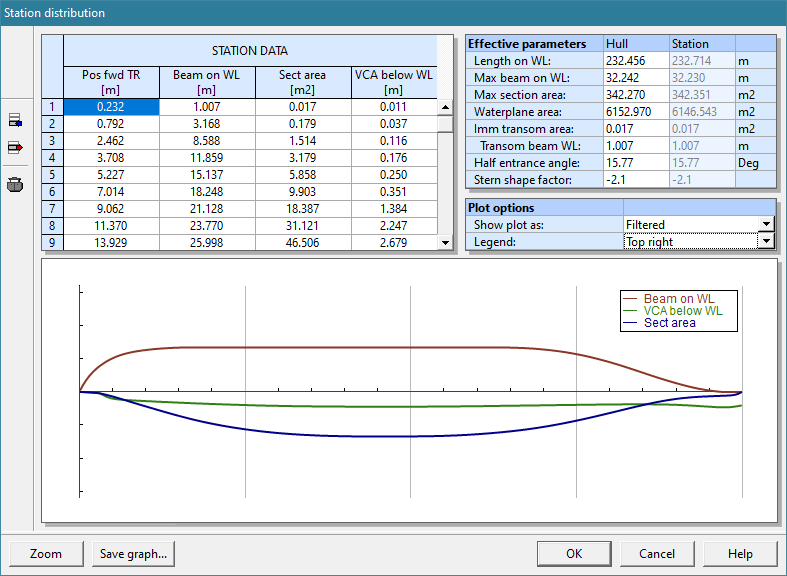
Figure 1 – “2D” data used for ADVM
Parametric (1D) methods are generally unsuitable for trim optimization. This is not surprising, as these methods are based on dimensional analysis of ships at their design waterline condition. Trimming a vessel distorts its parameters so that they fall outside the scope of the original data sets. (There are a few parametric methods that do consider stern-trimmed ballasted orientations, but these were for obsolete merchant cargo ship hull forms without bulbs and with simple stern shapes, so they do not represent contemporary vessels.)
NavCad’s ADVM (2D) method utilizes 3D hull CAD geometry (like CFD), but is able to provide predictions at a fraction of the resources required for CFD. It can be manipulated in different ways to account for sinkage and trim, which is critical for ships with flat transom sterns that may become immersed. While the ADVM method is certainly not a replacement for the many tasks and analyses that CFD can offer, it does provide a strong and cost-effective option for trim studies or benchmarking CFD.
For example, in the plot below of KSC predictions, we see that the ADVM method and CFD produced very similar qualitative outcomes. (Note that the ADVM did over-predict resistance, which we believe is due to an over-estimation of the form contribution in the method. A new viscous form drag model is under development to improve this for KCS-type vessels.) The parametric method (Holtrop) demonstrated good correlation to CFD at the design (zero trim) condition, but showed very little influence of trim on resistance.
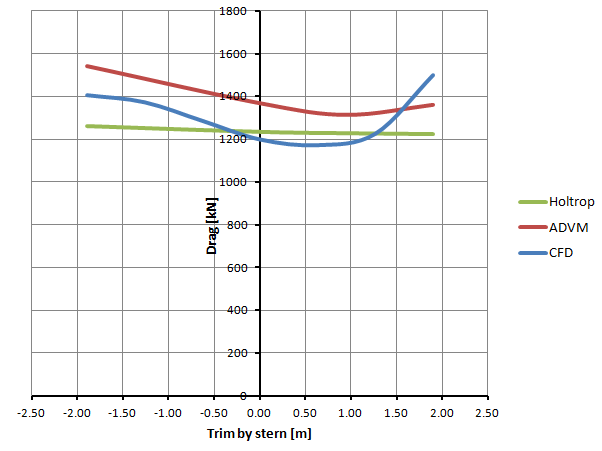
Figure 2 – Predictions for the KCS
Using a reduced-order calculation – such as the ADVM method in NavCad 2020 – is essential to an initial assessment of the benefits of trimmed operation and to narrow the scope of the design space if proceeding with higher-order CFD studies. Then the predicted resistance figures, whether by NavCad’s internal methods (such as ADVM) or external methods (such as CFD), can be extended to full fuel prediction as part of its Vessel-Propulsor-Drive system simulation.
Download the full article here: TNA-Oct-2020-Trim-Optimisation-using-NavCad-for-prediction-confidence.pdf