A two-part conversation with Bruce Hays and Larry Liebman (Orca 3D) and Don MacPherson (HydroComp)
In our previous story, we discussed at length the initial collaboration and humble beginnings between the HydroComp, Inc. and Orca3D LLC organizations. In Part 2, we examine more closely how HydroComp’s NavCad, the Orca3D naval architectural suite, and Orca3D Marine CFD provide a comprehensive toolchain for vessel design and performance analysis.
From the perspective of performance analysis, the Orca3D naval architectural suite has long offered a utility for quick concept-level resistance prediction, as well as a connector to NavCad for seamless data exchange and continuity of the design. “One of the hallmarks of NavCad is its breadth of different vessel types that it can handle,” states Bruce Hays, naval architect and Orca3D co-founder. “NavCad has been around for a long time,” offering full Vessel-Propulsor-Drive system analysis with its comprehensive library of prediction models for hulls and propulsors. Now, a deeper collaboration between the two companies is finding new ways to improve performance analysis via connection between NavCad and Orca3D Marine CFD. “I feel like we’re just scratching the surface in terms of our technical cooperation and really harnessing the power of the tools together.”
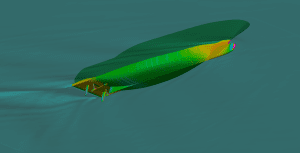
Figure 1: CFD simulation showing Dynamic Pressure.
Larry Leibman, fellow Orca3D LLC co-founder and naval architect, noted that, “We have plans that involve marrying the different fidelity prediction capabilities of the various tools. There are ways to leverage the different capabilities of both organizations to improve the end user’s ability to predict and improve the performance of their designs.”
There are several important components of a connection between NavCad and Orca3D Marine CFD, and Larry explains his perspective of the most crucial one. “In CFD, there are two different analyses you typically perform. One is simply towing the boat and evaluating its performance. The other one is moving the boat via some sort of propulsive force, something that generates thrust to move the boat, which is typically a propeller. While definition of a propeller performance specification is built into Orca3D, people typically have no idea what propeller to use. As you get into smaller boats and particularly down into the recreational boat industry, you’re picking an off-the-shelf propeller. NavCad has facilities that make propeller selection and performance definition for CFD a lot easier for users. I view that as probably the single-most beneficial component.”
Not only can NavCad provide the basic thrust and torque figures for self-propulsion analysis with Orca3D Marine CFD, it also now generates a largely missing piece to the propeller performance model – propeller lift force from shaft angle oblique effects. Using an oblique inflow correction feature (to account for forces created by the differing inflow seen by a propeller blade as it rotates at an oblique angle as shown in the image below), NavCad can export an enhanced KT-KQ data set that is now being applied in Orca3D Marine CFD. “The implication of not incorporating this propeller-generated stern lift force can be significant, particularly for planing craft,” comments Donald MacPherson, HydroComp’s Technical Director. “We all know how a stern lift force, such as from a trim tab or interceptor, can affect speed and even porpoising. Any prediction model that does not include oblique propeller effects can lead to inappropriate selection of propulsion equipment and client expectations.”
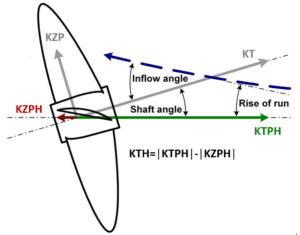
Figure 2: Oblique propeller effects.
Who benefits the most from this enhanced connection between NavCad and Orca3D Marine CFD? “Perhaps commercial small craft designers,” Bruce shares. “I think sometimes recreational production boat design doesn’t have the same contractual requirements as one-off commercial boat design that has a contractual speed, noise requirements, or emissions and efficiency standards.” Don adds, “All design agencies should benefit from performance analysis that better models the physics and forces involved, whether that be for specific vessels or for the strategic design requirements of production boatbuilders.”
Concerning industry trends, Larry believes NavCad is well-positioned to offer value to the electric boat market and envisions greater HydroComp-Orca3D collaboration along those lines. “Electric boats require a holistic approach, a systems-based approach to truly analyze performance. We see a lot of interest on our customer side.” NavCad includes propulsion drive features specifically for electric boats and submersibles, particularly in the ability to quickly create ‘generic motor’ models with limited data as well as to estimate realistic partial load efficiencies.
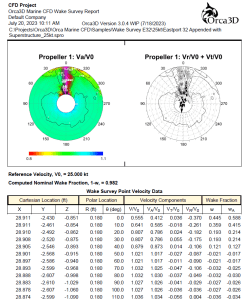
Figure 3: Example Propeller Wake Survey Report.
Harnessing the power of the expertise, resources, and commitment of both teams is aiding the development of innovative solutions meeting the needs of our customers – with a strong history and foundation, there is no stopping this dynamic duo. We invite you to join both Orca3D and HydroComp at the Orca3D Marine CFD Workshop at the IBEX Pre-Conference on September 30 in Tampa, Florida! Register here.
The Orca3D team will also be exhibiting during IBEX (October 1-3) at Booth 2-345. Email to make an appointment or stop by. Just like the early days, HydroComp staff will be alongside them. We look forward to seeing you and demonstrating all that you can accomplish with Orca3D and NavCad in your toolbelt!
Download this interview here.
For more information, contact:
HydroComp, Inc. Tel +1.603.868.3344 danielle.doonan@hydrocompinc.com www.hydrocompinc.com |
Orca3D Tel +1.410.696.3308 orca3d.com |