HydroComp staff recently participated in the American Society of Naval Engineers (ASNE) Multi-Agency Craft Conference 2018 in Baltimore, Maryland as one of ten competing teams in the Planing Hull Simulation Grand Challenge. As described by ASNE, the challenge was to computationally “simulate the Generic Prismatic Planing Hull (GPPH) in calm water” and predict resistance, heave, and trim for the subject vessel.
The participants, coming from commercial, academic, and government agencies, prepared simulations using hydrodynamic prediction tools from across a wide spectrum of methods and computational resources. For example, HydroComp’s flagship NavCad® software for resistance prediction and propulsion system simulation was run on a business-grade laptop. Many of the high-order tools, such as RANSE CFD codes, were hosted on extensive clusters.
The vessel chosen for the challenge was the NSWCCD “Generic Prismatic Planing Hull” (GPPH), as shown below. The hull represents a conventional planing craft with small chine flats and modest chine warp. The evaluation was conducted at its 7-foot model scale.

HydroComp intentionally used a “new user proxy” scenario for the NavCad simulation. A normal design office workflow was followed, with the assumption that the user had no detailed knowledge of data requirements or methodology. Only standard settings were used.
The enhanced implementation of the well-known Savitsky method in NavCad was determined to be suitable for the vessel, with all hull data automatically extracted from the CAD file. HydroComp is pleased to report that the simulation results were excellent, with resistance predicted within 1.8% of the model test figures – one of the best results demonstrated.
Vessel trim was slightly over-predicted (by less than half degree), but uniformly followed the model test results and was within the scatter of the other codes. Heave was also slightly over-predicted (by about 0.3 inches).
As expected, NavCad was the most computationally efficient tool demonstrated. Its computational demand of 0.1 CPU-hr was 11 times better than the next most efficient tool, and some 6 million times more efficient than the code with the greatest computational demand.
The success of NavCad at the ASNE MACC Planing Hull Simulation Grand Challenge underscores its critical value for the design of planing craft. Its predictive model is based on the equilibrium physics of planing, with high-fidelity prediction results. NavCad predictions can give users of higher-order codes the necessary “confidence benchmarks” for assurance that their data modeling, calculation settings, and simulation results are appropriate.
Rapid design space studies can allow higher-order codes to be applied to the most relevant design regime, with no waste investigating variations that can be easily dismissed. Remember, the most efficient analytical design is always based on the premise of “calculate what you need, not what you can”.
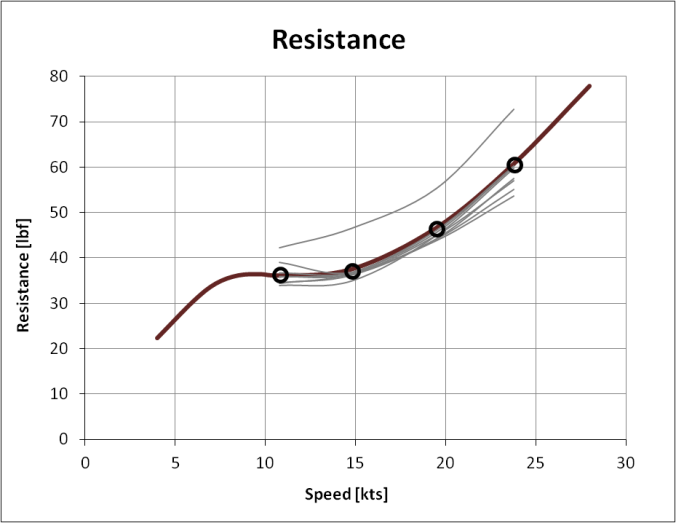
Resistance results
(The heavy line is the NavCad prediction. Markers are model test results. Thin grey lines are predictions by other teams.)
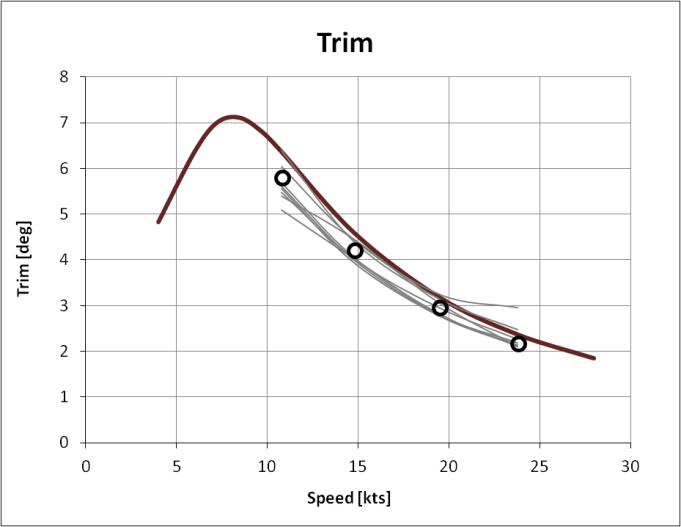
Trim results
13 Jenkins Ct, Suite 200
Durham, NH 03824 USA
Tel: (603)868-3344
Email: adam.kaplan@hydrocompinc.com
Download:
» NavCad Demonstrates Success